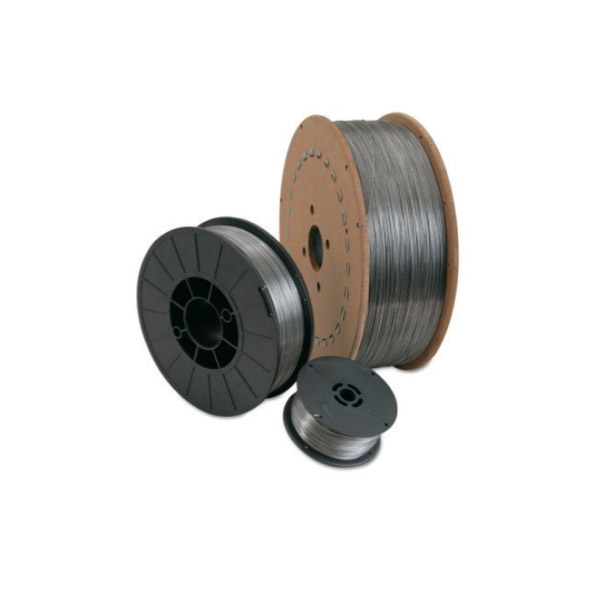
5356 aluminum welding wire, offered by Bob Martin Co., is known for its excellent corrosion resistance and high shear strength. It is widely used across various industries for both its mechanical properties and versatility in welding applications. Available in diameters ranging from 0.0300 to 0.1250 inches and conforming to the AWS A5.10 Class ER5356 specification, this wire is ideal for various demanding environments.
Chemical Composition
The typical chemistry of 5356 aluminum welding wire includes:
- Silicon (Si): 0.25 max
- Iron (Fe): 0.40 max
- Copper (Cu): 0.10 max
- Manganese (Mn): 0.05-0.20
- Magnesium (Mg): 4.50-5.50
- Chromium (Cr): 0.05-0.20
- Zinc (Zn): 0.10 max
- Aluminum (Al): Balance
- Titanium (Ti): 0.06-0.20
- Beryllium (Be): 0.0003 max
- Other Elements (OE): 0.05 max
- Other Elements Total (OET): 0.15 max
Available Forms: The wire is available in spool forms, making it convenient for continuous welding processes in various applications.
Industry Uses
Marine Industry
The marine industry extensively uses 5356 aluminum welding wire due to its superior corrosion resistance, which is crucial in saltwater environments. It is often employed in the construction and repair of ships, boats, and offshore platforms.
Aerospace Industry
In the aerospace sector, the wire’s high shear strength and resistance to stress corrosion cracking make it suitable for fabricating and repairing aircraft components. Its lightweight nature also contributes to the overall efficiency and performance of aerospace structures.
Automotive Industry
Automobile manufacturers use 5356 aluminum welding wire for assembling and repairing vehicle bodies, frames, and other components. Its strength and durability ensure long-lasting performance, even under rigorous operating conditions.
Construction Industry
For structural applications, the construction industry relies on 5356 aluminum welding wire to join aluminum frameworks, railings, and other architectural elements. Its resistance to weathering and corrosion makes it a preferred choice for both indoor and outdoor projects.
Manufacturing Industry
General manufacturing processes benefit from the versatility of 5356 aluminum welding wire. It is used in the production of various consumer goods, machinery, and equipment where strong, reliable welds are essential.
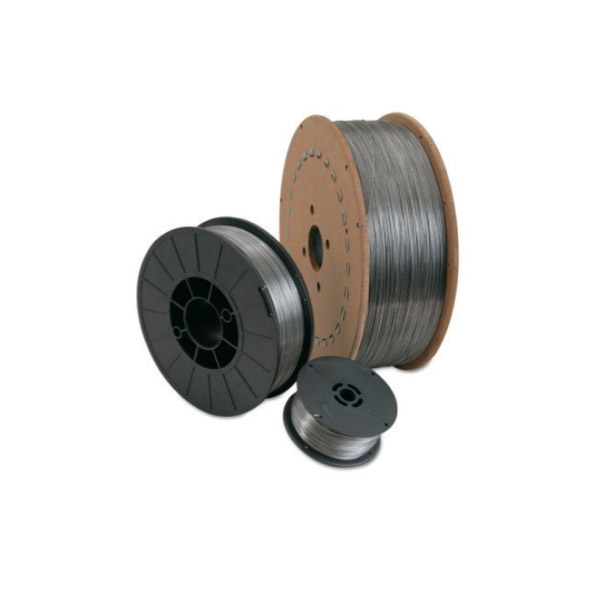
Benefits
1. Corrosion Resistance
The primary advantage of 5356 aluminum welding wire is its excellent resistance to corrosion, particularly in marine and other harsh environments. This property extends the lifespan of welded structures and reduces maintenance costs.
2. High Shear Strength
With a high shear strength, the wire provides robust and durable welds, capable of withstanding significant stress and mechanical loads. This is particularly beneficial in industries like aerospace and automotive, where structural integrity is paramount.
3. Versatility
The wide range of diameters available allows for flexibility in various welding applications, from thin sheet metals to thicker structural components. This versatility makes it a go-to option for many industries.
4. Ease of Use
5356 aluminum welding wire is designed to be user-friendly, with smooth feeding and minimal spatter during welding. This results in cleaner welds and higher productivity, making it a preferred choice for welders.
5. Compliance with Standards
Conforming to AWS A5.10 Class ER5356, the wire meets stringent quality and performance standards, ensuring reliability and consistency in every weld.
5356 aluminum welding wire from Bob Martin Co. stands out for its excellent corrosion resistance, high shear strength, and versatility, making it an essential material across various industries. Whether in the demanding marine environments or the high-performance aerospace sector, this welding wire delivers reliable and durable results, enhancing the quality and longevity of welded structures.