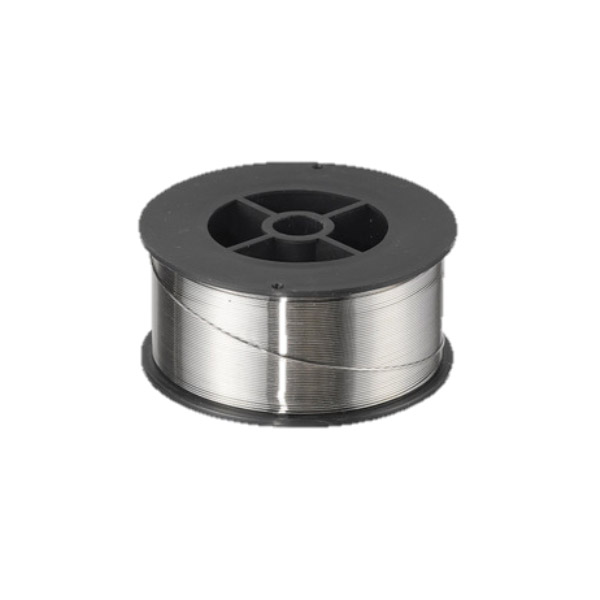
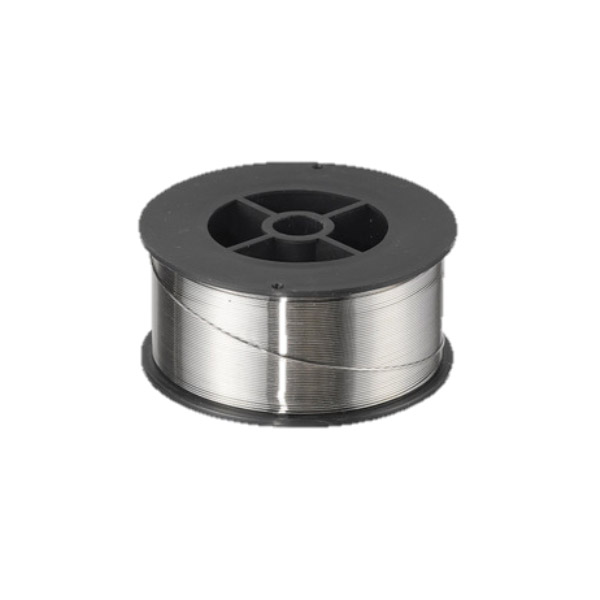
Nickel based alloys are used in RTD sensors, resistors, rheostats, voltage control relays, heating elements, potentiometers, and other components. Engineers design around properties unique to each alloy.
Nickel is a popular alloy for wires because its top layer can resist extreme chemical corrosion, including air and water oxidation. Nickel alloys are also resilient against acids and alkalis. Nickel wire is frequently used in products containing electrical components or those that experience high levels of heat (up to 2,600 °F). The material is also magnetic as long as it remains below 350 °F. Beyond this point, it will lose its magnetic properties.
The character traits of nickel alloys can sometimes be more useful than those of brass, copper, and beryllium. This is especially the case when using the wire outdoors. Nickel wire has the ability to resist corrosion at extremely high levels. It is able to resist oxidization from air and water, and it can withstand contact with acids and alkalis. The top layer of nickel is a protective layer, which protects the compound from chemicals. The process of creating this layer is called passivation. Nickel is considered a non-reactive metal that will dissolve slowly in acids.
Nickel wire is also commonly used for its ability to resist melting. Other metal alloys have a low melting point, but that is not the case for nickel. Nickel can withstand temperatures up to 2,600 degrees Fahrenheit (1,203 Celsius). The wire is also strong and it can withstand extensive wear and tear. It can also be stretched easily.
Nickel wires do have a strong magnetic property, but this is only the case when the wire has not been heated. Nickel wire will lose its magnetic abilities when heated to about 350 degrees Fahrenheit.