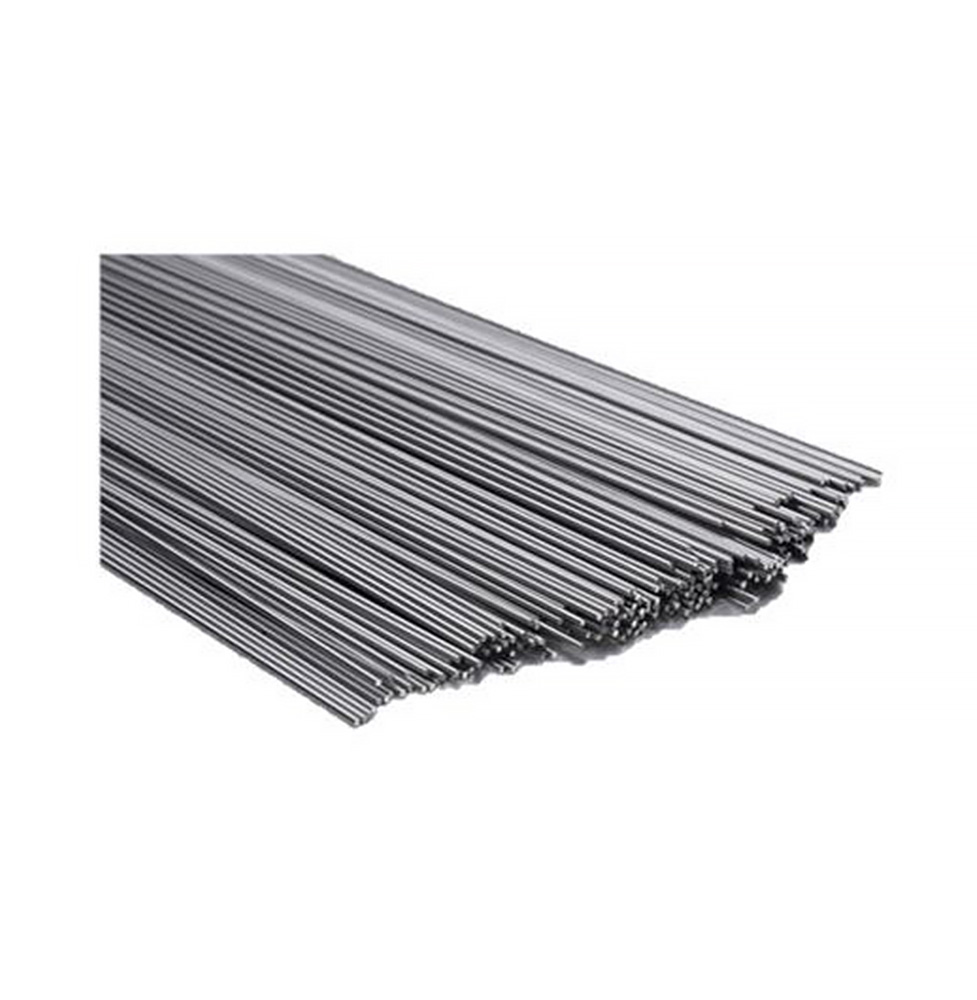
2319 alum was developed as a filler alloy for alloy 2219, widely used in high strength structural and aircraft applications. It has good resistance to stress corrosion. This alloy is heat treatable.
TIG Welding
It is typically used in the automotive industry, particularly for professional racing teams. It uses argon as a shielding gas and requires constant current equipment with AC capabilities. TIG aluminum welding does not need mechanical wire feeding. The welder feeds the filler material into a puddle. It is a clean procedure because the alternating current removes the aluminum’s oxidized layer, preventing contamination. Tungsten inert gas (TIG) welding or gas tungsten arc welding (GTAW) is a popular aluminum welding process.
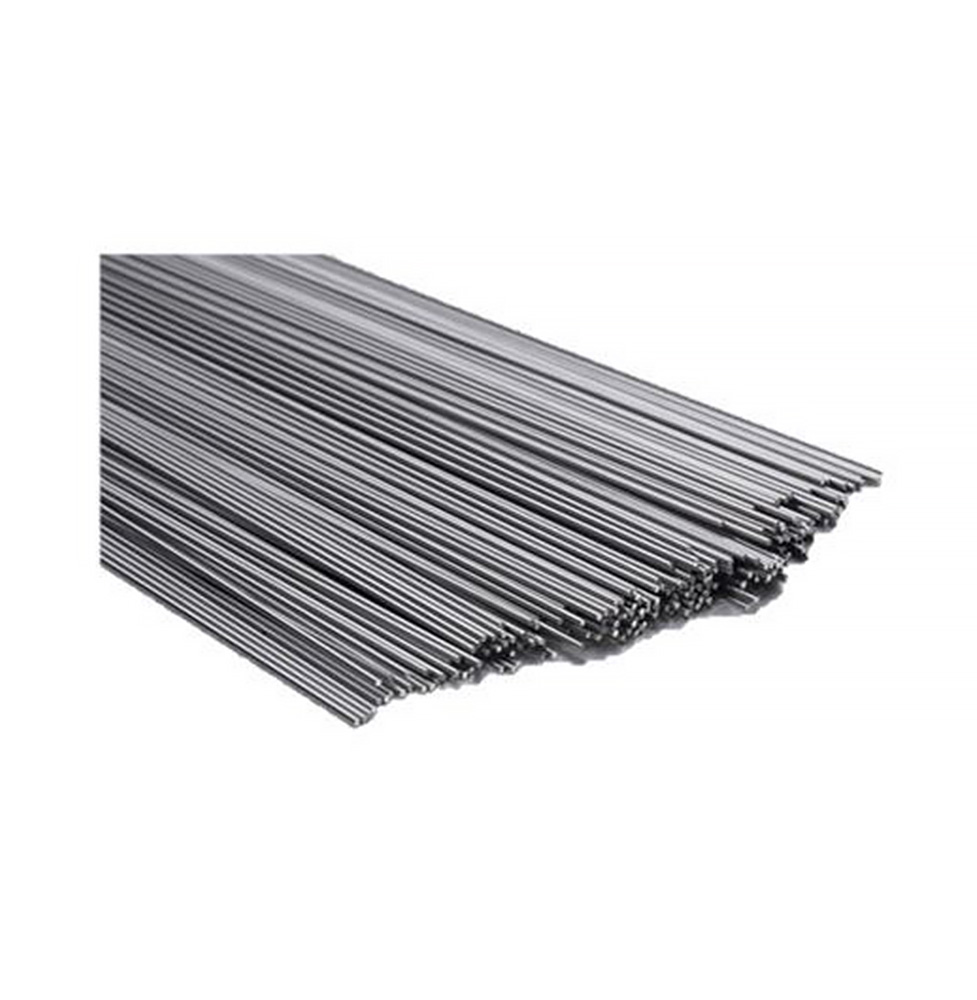
MIG Welding
Metal inert Gas (MIG) welding or gas metal arc welding (GMAW) is a common method for welding aluminum. It has higher deposition rates and faster travel speeds than TIG welding. However, it uses a mechanical wire feeding system, indicating that the welder may use a push-pull or spool gun to ensure wire feeding. To prevent aluminum from becoming porous, clean the filler rod and the base material, ensure they are moisture-free and have excellent shielding gas coverage.
Laser Beam Welding
Also known as electron beam welding, it requires an easily controlled and precise heat-affected zone, making it ideal for aluminum. It offers fast and clean welds and is appropriate for aluminum, which is prone to cracking.
Resistant Welding
This method joins metals by applying pressure and allowing a current to pass through the metal. It is wise to be cautious when using this welding technique because of aluminum’s high electrical and thermal conductivity.
Shielded Metal Arc Welding (SMAW)
This welding method is typically used to repair cast aluminum. It uses constant current equipment with an aluminum rod with electrode-positive polarity.
Contact us for questions about the many types of Aluminum welding wire that we offer.