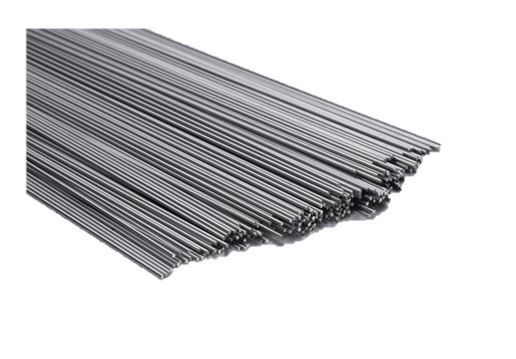
Learn more about welding step one from the following post and the welding steps two, three & four in the next post. Also check out the welding wire from Bob Martin Co. for your next project.
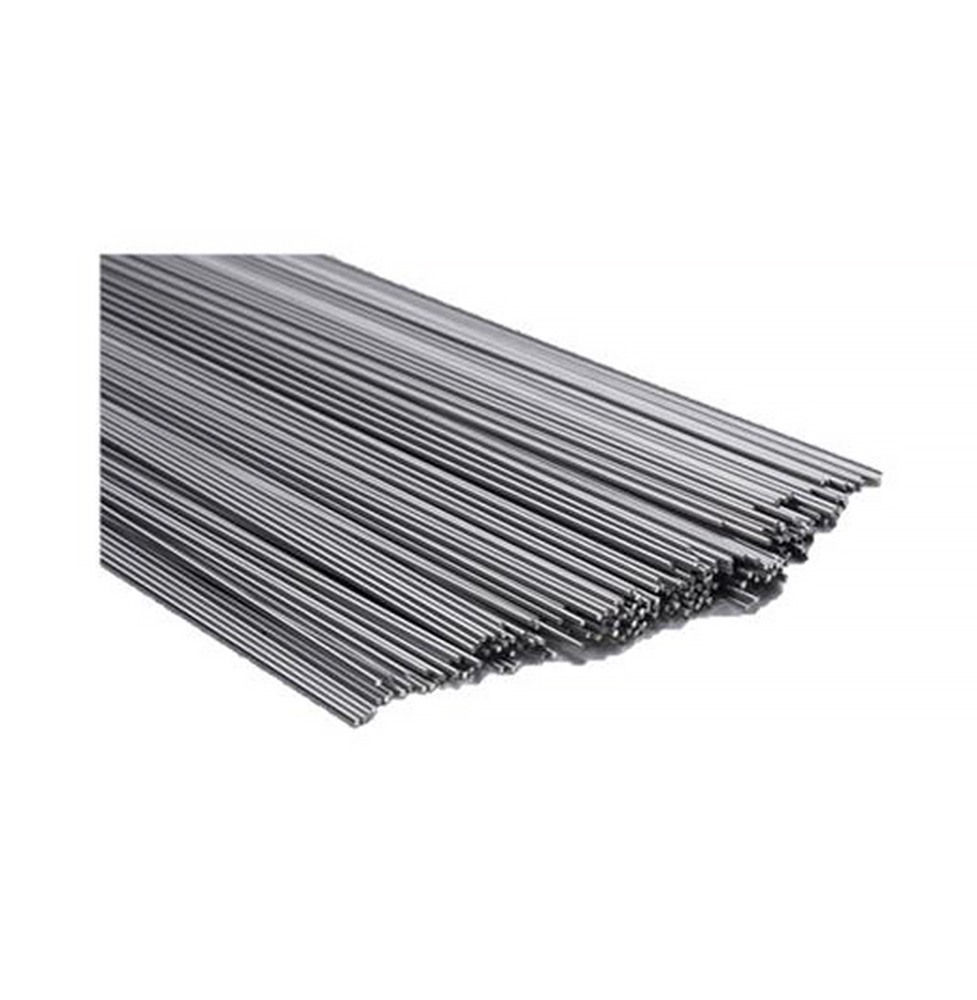
When both base metals are the same, use the base metal alloy as a guide. For example, if joining 316L to 316L, use 316L filler metal. Experience may show preferential corrosion in the weld, in which case, moving up in alloy content may be required. Careful consideration regarding how far to move up is necessary, so as not to over-alloy causing galvanic corrosion.
For dissimilar joint welding (example; Stainless Steel to Carbon Steel) Consideration: Failure can occur as a result of low alloy mixtures if the incorrect filler metal is selected, or if dilution rates are too high. The most common failure mode is cracking but weld embrittlement is also possible.
Proper alloy selection and welding technique are therefore important for a successful weld:
- DO NOT use low alloy electrodes to join low alloy to stainless steel. Brittle welds will result in this practice.
- DO NOT use lower alloyed stainless steel filler wire to join low alloy to stainless steel. Brittle welds will result in this practice due to martensite formation.
- DO USE over-alloyed grades such as 309 and 312 types, which are designed specifically for this purpose.
For dissimilar stainless to stainless or nickel to nickel joints see the dissimilar materials joining guide. Generally, best practice is to use the filler metal designed for the higher alloyed of the two. For example, if joining 304L to 316L base metals, use 316L filler metal.
When joining stainless steel to nickel base alloys always use nickel base filler metals.
- DO NOT use stainless steel filler metals for joining stainless steel to nickel base alloys as there is a high risk for centerline cracking. This is due to dilution out of the nickel side of the joint. Higher nickel in the stainless weld deposit creates an imbalance in the composition increasing the sensitivity to cracking.
Reference: https://www.esabna.com/us/en/education/blog/exaton-welding-guidelines.cfm